
Overview
Tech specs
Power
There is an on-board voltage regulator for higher voltages that protect the Braccio shield. NOTE: The protection doesn’t work for the Arduino Yun if you put the bridge between Vin and 5V on the Arm Robot Shield V1 (greater version of are called Braccio shield and has a power switch on the top of the shield)
Physical Characteristics
- Plastic Parts x 21
- Screws x 63
- Flat Washer x 16
- Hexagon Nut x 7
- Springs x 2
- Servo Motors: 2 x SR 311, 4 x SR 431
- Arduino compatible Shield x 1
- Power Supply 5V, 4A x 1
- Phillips Screwdriver x 1
- Spiral Cable Protection Wrap x 1
Fully assembled Braccio Kit:
Weight |
792 g |
Maximum operating distance range |
80 cm |
Maximum Height |
52 cm |
Base Width |
14 cm |
Gripper Width |
90 mm |
Cable length |
40 cm |
Load Capacity |
Maximum weight at 32 cm operating distance: 150 g |
Maximum weight at the minimal Braccio configuration: 400g |
Servo Technical Specification
SpringRC SR431 - Dual Output Servo |
|
Control Signal |
PWM Analog |
Torque |
@ 4.8V: 169.5 oz-in (12.2 kg-cm) @ 6.0V: 201.4 oz-in (14.5 kg-cm) |
Weight |
2.19 oz (62.0 g) |
Dimentions |
1.65×0.81×1.56 in (42.0×20.5×39.5 mm) |
Speed |
@ 4.8V: 0.20 sec/60° @ 6.0V: 0.18 sec/60° |
Rotation Support |
Dual Bearings |
Gear Material |
Metal |
Rotation Range |
180° |
Connector Type |
J (aka Futaba) |
SpringRC SR311 |
|
Control Signal |
PWM Analog |
Torque |
@ 4.8V: 43.13 oz-in (3.1 kg-cm) @ 6.0V: 52.86 oz-in (3.8 kg-cm) |
Weight |
0.95 oz (27.0 g) |
Dimentions |
1.23×0.65×1.13 in (31.3×16.5×28.6 mm) |
Speed |
@ 4.8V: 0.14 sec/60° @ 6.0V: 0.12 sec/60° |
Rotation Support |
Dual Bearings |
Gear Material |
Metal |
Rotation Range |
180° |
Connector Type |
J (aka Futaba) |
Conformities
Documentation
Assembly video
OSH: Schematics
The TinkerKit braccio is open-source hardware! You can build your own board using the following file:
Get Inspired
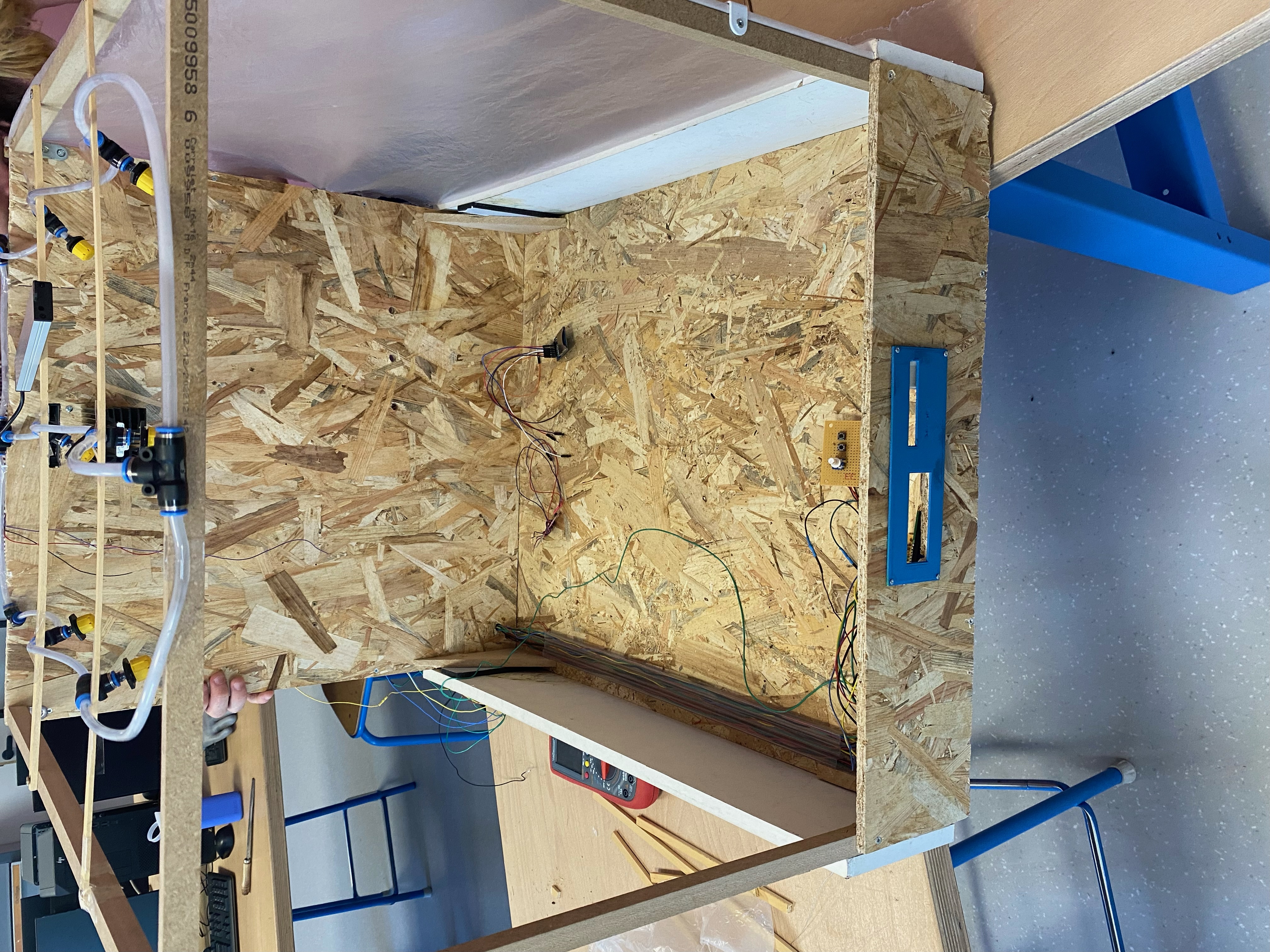
Just a simple and enjoyable autonomous greenhouse
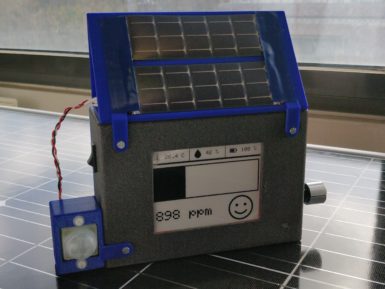
Humans are animals and like all animals, we evolved in mostly outdoor conditions where the air is nice and fresh. But modern society keeps most of us indoors the vast majority of the time, which could have negative health effects. There are many potential hazards, including a lack of sunlight and psychological effects, but CO2 may pose a more tangible risk. To keep tabs on that risk within classrooms, a team from Polytech Sorbonne built this small CO2 monitor. This CO2 monitor performs two functions: it shows anyone nearby the CO2 levels in the area and it uploads that data over LoRaWAN to a central hub that can track the levels across many locations. A school could, for example, put one of these CO2 monitors in every classroom. An administrator could then see the CO2 levels in every room in real time, along with historical records. That would alert them to immediate dangers and to long term trends. At the heart of this CO2 monitor is an Arduino MKR WAN 1310 development board, which has built-in LoRa® connectivity. It uses a Seeed Studio Grove CO2, temperature, and humidity sensor to monitor local conditions. To keep power consumption to a minimum, the data displays on an e-ink screen and an Adafruit TPL5110 timer only wakes the device up every ten minutes for an update. Power comes from a lithium-ion battery pack, with a DFRobot solar charger topping up the juice. It uploads data through The Things Network to a PlatformIO web interface. An Edge Impulse machine learning model detects anomalies, so it can sound a warning even if nobody is watching. The enclosure is 3D-printable.
FAQs
How many axis does the Braccio robot arm have?
The braccio has a total of 6 axis:
Axis 1 – It is located at the base of a robot, and helps it to rotate from left to right.
Axis 2 – It helps the lower arm of a robot to move in an up and down motion.
Axis 3 – It allows the upper arm of a robot to move forward and backward.
Axis 4 – This axis is known as wrist roll, and it rotates the upper arm of a robot in a circular movement.
Axis 5 – It permits the wrist of the robot’s arm to raise and lower.
Axis 6 – It allows the wrist of the robot’s arm to rotate freely in a circular motion.
All the above six axes are controlled with the help of servo motors.